Physical and Chemical Reaction during Firing of Sanitaryware
Firing is the final and important process in sanitaryware production. Firing of sanitaryware can be done in shuttle kiln and also Tunnel kiln. Conversion of low strength product into high strength, durable & chemical resistance product is achieved during firing. Sanitary ware firing temperature can go up to 1220ºC. It various according to the composition of raw materials used.
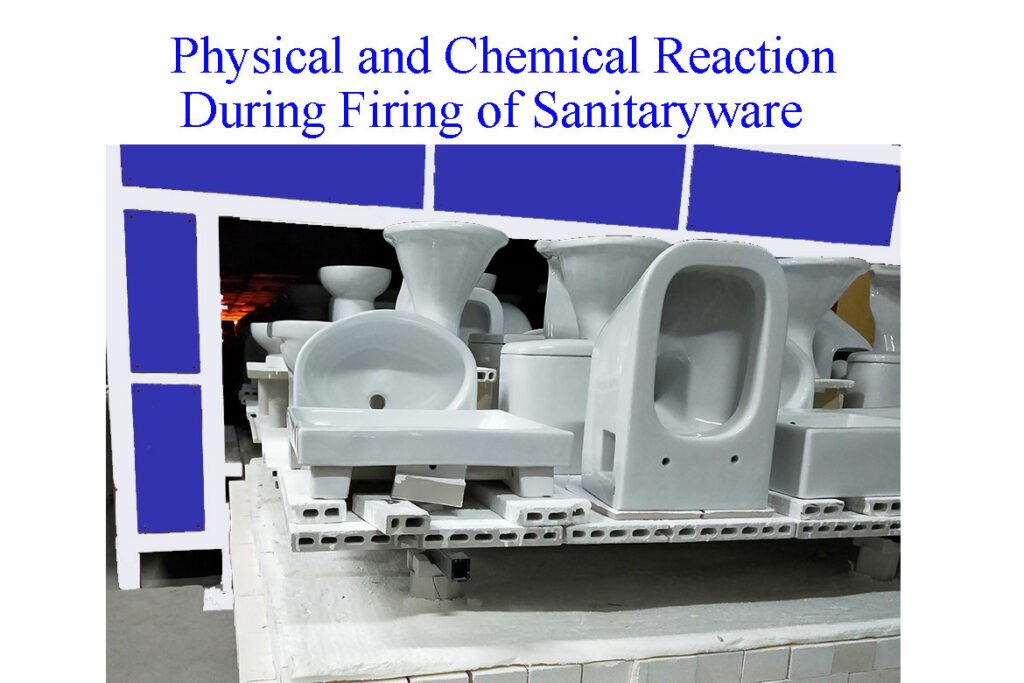
Introduction of sanitaryware firing:
Learning firing physical and chemical changes at different temperature will help to understand the firing cycle better and help to control the defects or faulty happening in firing cycle and also helps to reduce the firing cycle process. The physical and chemical reaction during firing are depends upon four major factors. Those are :
1) Particles size of raw materials.
2) Composition of body and glaze.
3) Rate at which the ware are heated and cooled
4) Soaking time at various temperature
Kiln used on sanitaryware:
Normally two types of kin used in sanitary ware manufacturing industry. Those are tunnel Kiln and shuttle kiln.
Tunnel kiln:
Tunnel kiln is continuous kilns that are used in sanitaryware manufacturing industry. This kiln made up of straight tunnel with an arched or a flat top. These kilns are used in first firing cycle.
Shuttle kiln:
Shuttle kiln is a chambers kiln that is used in sanitary ware manufacturing industry. Normally these kilns are used for re-fire purpose.
Physical and Chemical Reactions:
Following physical and chemical changes happens during firing of sanitary ware body in kiln.
- Dehydration.
- Decomposition.
- Combustion.
- Dissociation.
- Fusion.
- Solution.
- Reaction.
- Changes of structure.
Heating Period:
30ºC to 150 ºC – In this stage mechanically combined water from the wares are removed. Normally before firing the wares can be preheated to make this process more easy and fast. The ware should not contain more than 1.5% of moisture content, and heating must be carried out too slowly to avoid bursting of piece. After this stage piece should not contain more than 1% of moisture.
150ºC to 500ºC
In this temperature decomposition of Organic materials begin. All carbonaceous materials present in the raw materials starts to begin decompose. The rate at which heating is carried out should be able to decompose and burn the organic materials in the body. The rate of heating is indirectly propositional to the rate of firing. The thickness of the wares increases than the heating rate should be lowered.
500ºC -700ºC
At this temperature hygroscopic and chemically combined water from the wares are dehydrated. Conversion of silica from alpha form to beta form happens at the temperature around 573 ºC. Decomposition of carbonates and biotitic micas in clay also happens in this stage.
700ºC -1050ºC
Magnesium and calcium carbonate in ceramic wares starts to decompose.
950ºC – 1100ºC
In this temperate shrinkage of body starts. The glaze also starts melting.
1100ºC – 1250ºC
In this high temperature silica melts and forms glass. High shrinkage happens at this stage. Lot of gases is escapes through melted glass surface. A definite soaking time is given to even out the temperature in all area of the sanitary ware body and glaze.
Cooling period
1250ºC – 1200ºC
Still some trapped gas formed in firing will be allowed to escape. Normally rate of cooling at this level is kept very low to make sure all gas escapes before rapid cooling.
1200ºC – 800ºC
This stage is called as sudden/rapid cooling stage. To achieve the glass effect in glaze surface this sudden cooling is carried out.
800ºC – 600ºC
At this temperature slow cooling is carried out to even out the body temperature at different areas. Because quartz conversion will takes place after this stage.
600ºC to 500ºC
At this phase conversion of quartz beta to alpha happens.
500 ºC to 30 ºC
In this temperature only cooling of ware happen. Other than cooling nothing really happens.
Example curve of sanitaryware firing cycle:
Below curve is a fast firing cycle in shuttle kiln. This fast firing cycle time is 17 Hours. This is first firing in sanitary ware production.
Example curve of sanitaryware firing cycle[/caption]
Sanitary ware firing Defects- Remedies:
Belching of coloured ware – Firing happened at reduction atmosphere. Insufficient air supply is given to the kiln.
Black Core – Insufficient soaking temperature during firing. Organic-rich raw materials are used.
Less glossiness – Some of the reasons for less glossiness are insufficient firing, devitrification of glaze.
Bloating of wares – this defect happens when the thickness of the body is high so the evolved gas cant able to escape from the ware.
Dunting – Fast firing up to 700 ºC. Temperature uniformity varies at the different area of the wares. Have a look at 25 Defects in sanitaryware manufacturing.
Conclusion:
This site is especially dedicated for sanitary ware professionals. Please leave your comment about this article below.
Firing is the final and important process in sanitaryware production. Firing of sanitaryware can be done in shuttle kiln and also Tunnel kiln. Conversion of low strength product into high strength, durable & chemical resistance product is achieved during firing. Sanitary ware firing temperature can go up to 1220ºC. It various according to the composition of raw materials used.
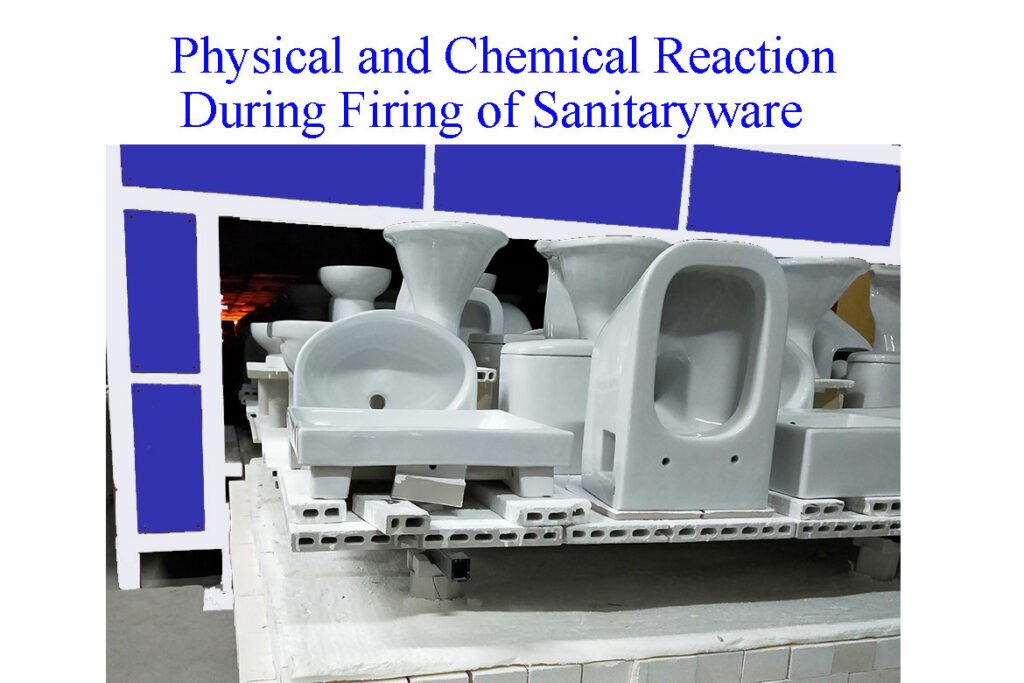
Introduction of sanitaryware firing:
Learning firing physical and chemical changes at different temperature will help to understand the firing cycle better and help to control the defects or faulty happening in firing cycle and also helps to reduce the firing cycle process. The physical and chemical reaction during firing are depends upon four major factors. Those are :
1) Particles size of raw materials.
2) Composition of body and glaze.
3) Rate at which the ware are heated and cooled
4) Soaking time at various temperature
Kiln used on sanitaryware:
Normally two types of kin used in sanitary ware manufacturing industry. Those are tunnel Kiln and shuttle kiln.
Tunnel kiln:
Tunnel kiln is continuous kilns that are used in sanitaryware manufacturing industry. This kiln made up of straight tunnel with an arched or a flat top. These kilns are used in first firing cycle.
Shuttle kiln:
Shuttle kiln is a chambers kiln that is used in sanitary ware manufacturing industry. Normally these kilns are used for re-fire purpose.
Physical and Chemical Reactions:
Following physical and chemical changes happens during firing of sanitary ware body in kiln.
- Dehydration.
- Decomposition.
- Combustion.
- Dissociation.
- Fusion.
- Solution.
- Reaction.
- Changes of structure.
Heating Period:
30ºC to 150 ºC – In this stage mechanically combined water from the wares are removed. Normally before firing the wares can be preheated to make this process more easy and fast. The ware should not contain more than 1.5% of moisture content, and heating must be carried out too slowly to avoid bursting of piece. After this stage piece should not contain more than 1% of moisture.
150ºC to 500ºC
In this temperature decomposition of Organic materials begin. All carbonaceous materials present in the raw materials starts to begin decompose. The rate at which heating is carried out should be able to decompose and burn the organic materials in the body. The rate of heating is indirectly propositional to the rate of firing. The thickness of the wares increases than the heating rate should be lowered.
500ºC -700ºC
At this temperature hygroscopic and chemically combined water from the wares are dehydrated. Conversion of silica from alpha form to beta form happens at the temperature around 573 ºC. Decomposition of carbonates and biotitic micas in clay also happens in this stage.
700ºC -1050ºC
Magnesium and calcium carbonate in ceramic wares starts to decompose.
950ºC – 1100ºC
In this temperate shrinkage of body starts. The glaze also starts melting.
1100ºC – 1250ºC
In this high temperature silica melts and forms glass. High shrinkage happens at this stage. Lot of gases is escapes through melted glass surface. A definite soaking time is given to even out the temperature in all area of the sanitary ware body and glaze.
Cooling period
1250ºC – 1200ºC
Still some trapped gas formed in firing will be allowed to escape. Normally rate of cooling at this level is kept very low to make sure all gas escapes before rapid cooling.
1200ºC – 800ºC
This stage is called as sudden/rapid cooling stage. To achieve the glass effect in glaze surface this sudden cooling is carried out.
800ºC – 600ºC
At this temperature slow cooling is carried out to even out the body temperature at different areas. Because quartz conversion will takes place after this stage.
600ºC to 500ºC
At this phase conversion of quartz beta to alpha happens.
500 ºC to 30 ºC
In this temperature only cooling of ware happen. Other than cooling nothing really happens.
Example curve of sanitaryware firing cycle:
Below curve is a fast firing cycle in shuttle kiln. This fast firing cycle time is 17 Hours. This is first firing in sanitary ware production.
Example curve of sanitaryware firing cycle[/caption]
Sanitary ware firing Defects- Remedies:
Belching of coloured ware – Firing happened at reduction atmosphere. Insufficient air supply is given to the kiln.
Black Core – Insufficient soaking temperature during firing. Organic-rich raw materials are used.
Less glossiness – Some of the reasons for less glossiness are insufficient firing, devitrification of glaze.
Bloating of wares – this defect happens when the thickness of the body is high so the evolved gas cant able to escape from the ware.
Dunting – Fast firing up to 700 ºC. Temperature uniformity varies at the different area of the wares. Have a look at 25 Defects in sanitaryware manufacturing.
Conclusion:
This site is especially dedicated for sanitary ware professionals. Please leave your comment about this article below.
Written by : Venkat Mani
Venkat Mani is a Ceramic Engineering Graduate from India, working in Sanitaryware production line for 15 years. He shares Meaningful content related to sanitaryware professionals that others find useful.
5s Comments
Leave A Comment
A quick overview of the topics covered in this article.
- Introduction of sanitaryware firing:
- Kiln used on sanitaryware:
- Physical and Chemical Reactions:
- Example curve of sanitaryware firing cycle:
- Sanitary ware firing Defects- Remedies:
- Conclusion:
- Introduction of sanitaryware firing:
- Kiln used on sanitaryware:
- Physical and Chemical Reactions:
- Example curve of sanitaryware firing cycle:
- Sanitary ware firing Defects- Remedies:
- Conclusion:
Hello sir
I am abhimannu from bolpur santinikatan .
Very good site for education.
Your article was really useful. I have an interview in 2 dayswhere the position is Firing Engineer GET. Now I want to know what kind of interview questions can be asked to me related to firing in sanitary ware.
Your guidance will be much helpful to me.
Thank you
Thanks you dear Mani for your valuble input.
Hello, During the heating and cooling period, how long should each stage within the period take?
For example how many minutes or hours should the heating period between 500⁰C to 700⁰C take?
Great as usual