9 Elements In Sanitaryware Production Cost:
In sanitaryware the product cost if calculated based on the Cost per Kg. Monthly production cost are important to understand production efficiency and improve.
To improve one must look into the closely the number element wise. This help to understand why and how to reduce the cost. Todays competitive price sensitive market, production cost the basis of product cost. So in this article we will deep dive into elements in sanitaryware production cost and discuss one by one.
A simple production cost calculation is the total spending cost on the all below elements divided by the Total Kg produced and sent to Packing is cost per Kg.
Cost per Kg= Total Spending on Production Elements/Total Kg Produced and Sent to Packing
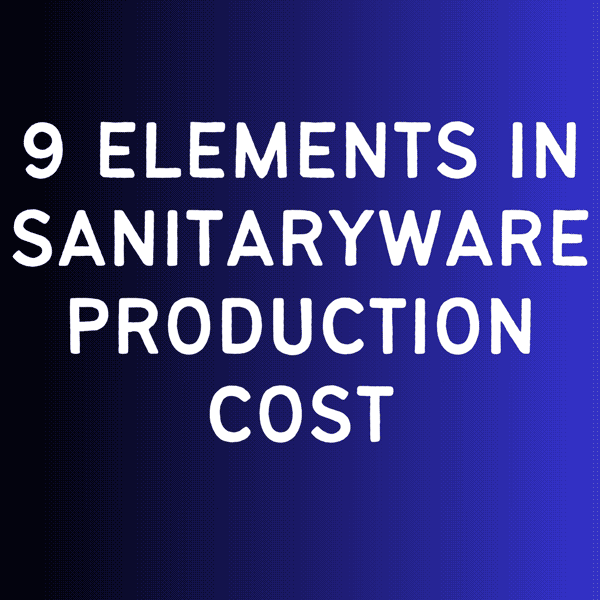
Following are the elements in the Sanitaryware production cost,
Raw Material Cost:
Raw material cost are the first element in the production cost. This raw materials can be divided in to three section. They are, 1) Raw materials for Slip. 2) Raw materials for Glaze. 3) Plaster Cost.
Having separate Material Cost for Slip, Material Cost for Glaze, Material cost for Plaster will help to understand where is cost going on per Kg.
The cost is total consumed per month considering stock.
Man Power Cost:
All labor Cost and Production Staff will come inside the production cost as a man power cost. As sanitaryware is labor intense manufacturing, normally around 30-40% of the production cost will from this Element. It will vary based on the automation level.
The labor cost methods varies based on the type of contract, Generally good infra structured & technically strong companies use permanent or contract labors. Second type is Piece Rate payment labors. Labor get paid for the output the provide. These are companies that does not have quality control in palace to maintain quality, so they outsource the labor work.
Comparing both the type of man power cost, the Piece rate payment method is higher in cost.
Energy Cost:
Power & Fuel Cost are the energy cost elements in the Sanitaryware production process. This is another major cost factor in the sanitaryware cost per kg.
Compared to other elements, energy costs exhibit significant fluctuations from one country to another. Countries with significant oil exports tend to have lower percentages of energy costs.
Consumable Cost:
Every day Consumable items like Sponge, Scoring pad, Gloves and etc. are one of the cost element in the Production. Avoiding wastage and Maximizing the Consumables will help to Reduce the cost.
Providing Proper consumables to get the High Firing yield will provide over all reduced cost of the production.
Maintenances Cost:
All Cost of machine Spare parts materials, Labor cost related to Maintenance, scheduled maintenance cost, outsourcing Cost of machines maintenance, Consumables related to maintenance like oil and etc are included into this cost elements.
Doing preventive maintenance to avoid emergency breakdown will help to reduce the overall production cost as well as Maintenance cost.
Maintenance Service cost can be amortized to get the proper cost element. For Example, Air compressor service with the interval of 6 months can be divided into six months and added to the production cost.
Other cost:
Any Cost associated with water is included in the water cost element.
Recycling of water related water treatment also will be added to this section or some companies will add this cost to the maintenance cost.
Conclusion:
In total, we can see 9 cost element are present in the sanitaryware production cost. 1) Body Raw material cost, 2) Glaze raw materials cost, 3) Plaster cost , 4) Labor cost, 5) Fuel cost, 6) Power cost, 7) Consumable cost, 8) Maintenance cost and 9) water cost. By analysis this cost elements can be reduced and optimized.
Written by : Venkat Mani
Venkat Mani is a Ceramic Engineering Graduate from India, working in Sanitaryware production line for 15 years. He shares Meaningful content related to sanitaryware professionals that others find useful.
In sanitaryware the product cost if calculated based on the Cost per Kg. Monthly production cost are important to understand
A quick overview of the topics covered in this article.