Investment for New Sanitaryware Factory: Key Consideration
A well researched proper budgeting is required for any new sanitaryware factory to sustain market competition and financial viability of the project. Following factors needs to be considered to get accurate new sanitaryware factory investment required for erection.
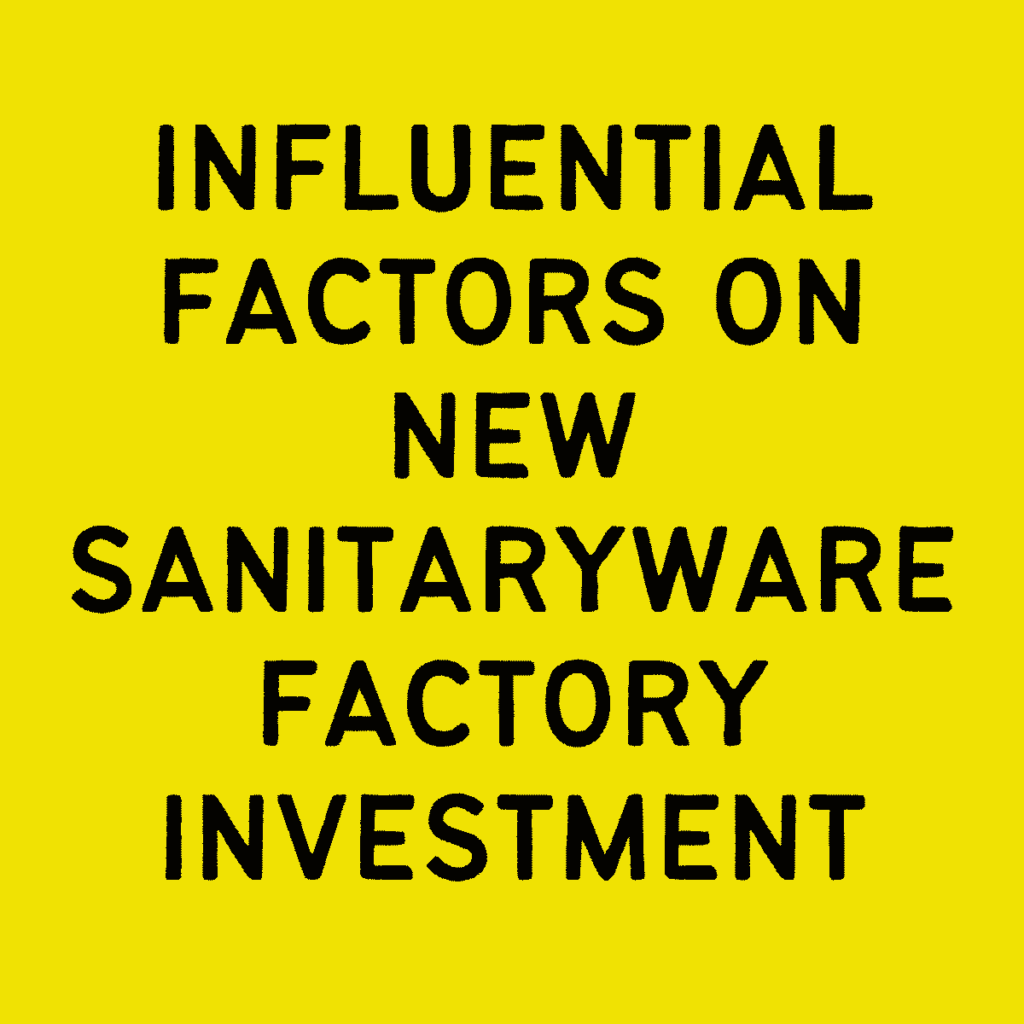
Automation Level:
- Everyone love automation because of the issues associated with the man power. It Is important to bring the level of automation where it can reduce production cost as well as higher quality.
- In sanitaryware industry the cost of automation is very high, almost 3 times the manual. and the automation is recommended when the production capacity is very high( Above 5000 Pcs per day).
- Automation also required operators with skill to operate machines. Semi automation provides better Investment option for current sanitaryware Industry.
- Consider Semi-automation and gradually incorporate more automation will help to understand better return on investment.
- If labor intense location, consider full manual production to reduce initial cost and cost of production.
- High levels of automation are recommended primarily in areas where there is a scarcity of labor and where the cost of energy is low.
Expansion Requirement:
- During planning stage always consider the future expansion requirement of sanitaryware factory.
- Ensure to have sufficient space for equipment and machinery in the plant layout for future expansion.
- Plan Equipment capacity required based on the future plan, always have minimum 2 sets of machinery to allocate the total capacity of the factory to reduce breakdown effect on the production.
- Plan for Sample/Trial production line with equipment and machinery in Slip, Glaze & Casting departments.
Kiln Requirement:
- Based on the planned capacity of the factory plan for the Kiln.
- If the Planned capacity less than 600Pcs per day plan for a only Shuttle kiln.
- If the planned capacity or the future capacity is more than 2000 Pieces first install shuttle kiln and then go for a tunnel kiln. this will help to stabilize the production first year.
- Only if you expect to have production capacity stable for a tunnel kiln, then go for tunnel kiln only. But this plan only helps to reduce Investment cost. In long run having shuttle kill always help when sudden downsizing production.
- I would suggest go for a shuttle kiln if have investment, all reputed sanitaryware brands having both kilns to manage sanitaryware production process.
Regulatory Compliance Machineries:
- There are some machineries required to meet government regulatory compliance.
- Air leak test machine to check the leak test for toilets.
- Trap glaze machine for glaze the trap way area of the water closet.
- Rim glaze gun for spray under the rim of water closet.
- Above are some of the examples to have proper machineries to produce products that meets the market requirement.
Raw Materials Processing:
- When creating an investment plan, it’s important to consider multiple options for raw material processing units. This approach can help reduce environmental impact. Here are a few options:
- The first option is using a pitcher machine to crush and reuse rejected products from the process as raw material. This method promotes recycling within the production cycle, reducing waste and the need for new raw materials.
- The second option involves using a sludge kiln to fire the sludge and remove organic impurities. The fired sludge can then be reused as a raw material in the body of the products. This process not only minimizes waste but also ensures that the materials are purified and suitable for reuse in production.
Turnkey Company Or Inhouse Team:
- For erection of sanitaryware factory there are two option one can go. One is give the project to Turnkey company or hire and use a Inhouse Technical team. Both options have their advantages and disadvantages.
- Here is a comparison table,
Turnkey Company | Inhouse Team |
---|---|
Much faster to Start the project and Finish. | Takes time for planning and finding suppliers and finish the erection. |
One company to Handle From planning to Execution. | Inhouse team needs to have Ceramic technician as well as Electrical & mechanical Technicians. |
Modifying the plan in middle is difficult. | Management will have full control over the project customization. |
Cost of investment will be high as all the machinery and equipment will have extra margin as they procure from other companies. | Can save 30% up to investment by procuring the machinery from direct using inhouse team. |
Responsible only until the project is handed over. | Inhouse team will have responsibility to bring quality production as well as maintain the standards. |
Good to have a inhouse team and source part of the project from companies will have a great combination factor for investment as well as factory efficiency. .
Quality Control System:
- Investing good infrastructure for quality control system and defect analyzing system will go long way in the sanitaryware factory.
- Cost of production is completely depend on the defects reduction, so investing to understand the defect and severity is vital.
- Invest for software and touch screen defect recording system.
- If required plan to invest on the barcode tracking system, completely depends on the location and culture of the factory.
Conclusion:
While Planning and budgeting for new sanitaryware factory investment always consider the above points for long term goal of achieving low cost of production with high quality standard products. A factory can survive long term Only it achieves both the goal of high quality with low cost product. So budget accordingly your investment to achieve.
You can contact me for technical consulting info@sanitaryware.info or WhatsApp/Call = +91-9500693318. Also look at the how to start sanitaryware manufacturing factory.
Written by : Venkat Mani
Venkat Mani is a Ceramic Engineering Graduate from India, working in Sanitaryware production line for 15 years. He shares Meaningful content related to sanitaryware professionals that others find useful.
A well researched proper budgeting is required for any new sanitaryware factory to sustain market competition and financial viability of
A quick overview of the topics covered in this article.